Press'O sensor
Presentation
The Press'O sensor is a LoRaWAN class A sensor that manages two different power supplies: one is external and may range from 9V to 24V, the other one is internal on the battery. The Press'O sensor incorporates 2 analog inputs, 1 digital input and 1 output power source (configurable in 10V or 14V and in duration from 0 to x ms, by default 125ms). It also includes an internal antenna.

Family code / Release Note
The family code of Press'o devices is: 50-70-017-(005 and upper) or 50-70-189 [with external antenna] For 50-70-017-004 and lower see older revision documentationRelease note:
- 50-70-017-006: new casing, battery holder, output power selection
LoRaWAN release
v1.0.2 Region Parameter rev BElectronic specification
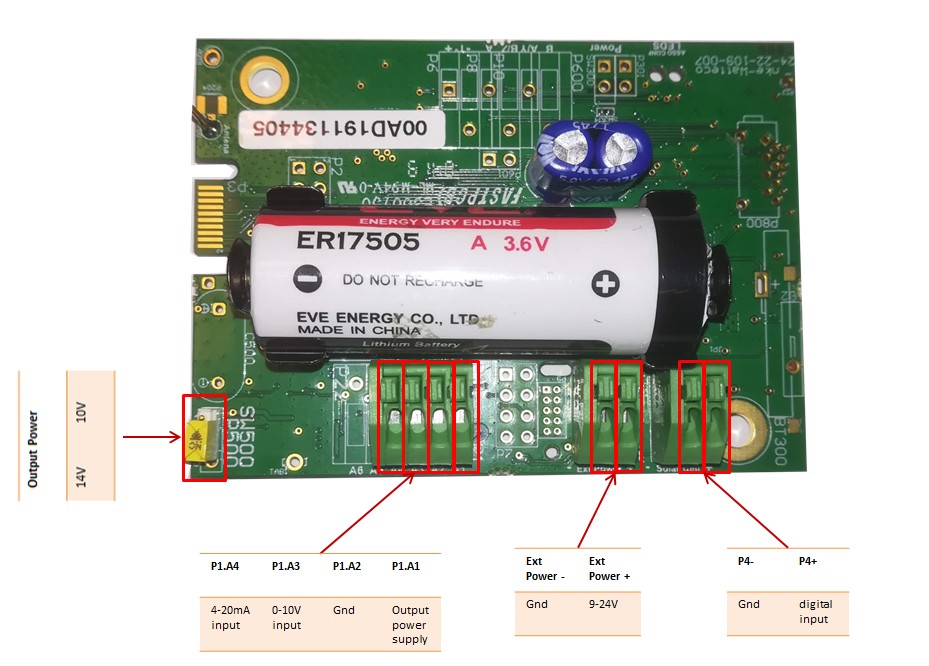
4-20 mA mode
• In the 4-20 mA mode, it is better to use 10V output power supply. The V+ (power supply of the external probe) is powered during 120ms by default.
• To add an external power supply, make the following connections:
• A series connection can be made with the Press'O and another reader (external sensor) with a 4-20mA input.
0-10 V mode
In the 0-10V mode, the V+ (power supply of the external sensor) is powered during 120ms by default:
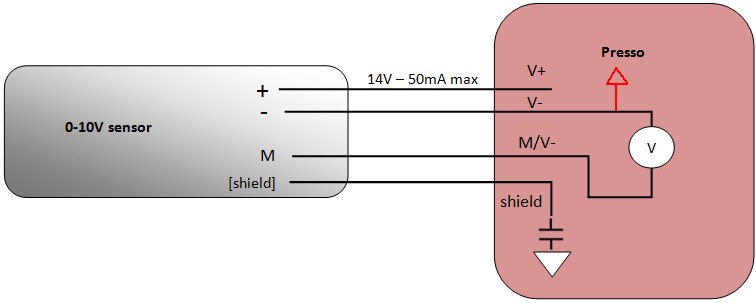
On the Press'O: V+ is the output power supply, V- is the ground, M is the measurement input.
On the sensor: + is the input power supply , - is the ground, and M is the measurement output.
Installation and operation
Installation
The housing is intended to be installed inside or outside a building but it must be protected from vertical water spray and direct sunlight. The product is delivered disassembled. This enables the connection to the screw terminals. Before connecting your cable strands to the product’s screw terminals, you must insert the cable gland's nut and the seal.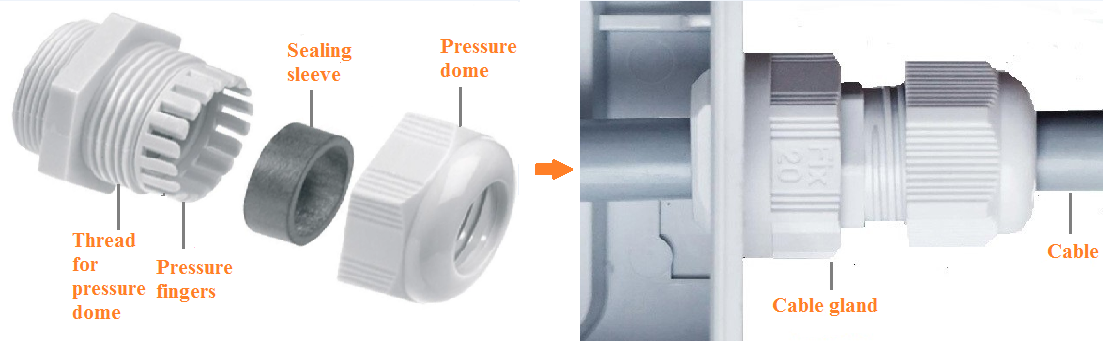
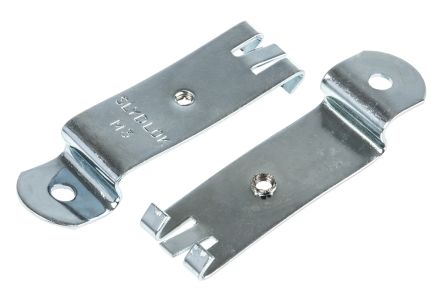
Radio propagation
In order for the sensor to operate correctly, the number of obstacles should be limited in order to avoid excessive radio wave attenuation. It is also important to place the sensor as high as possible. The Press'O sensor has 3 cable glands, which should be positioned horizontally.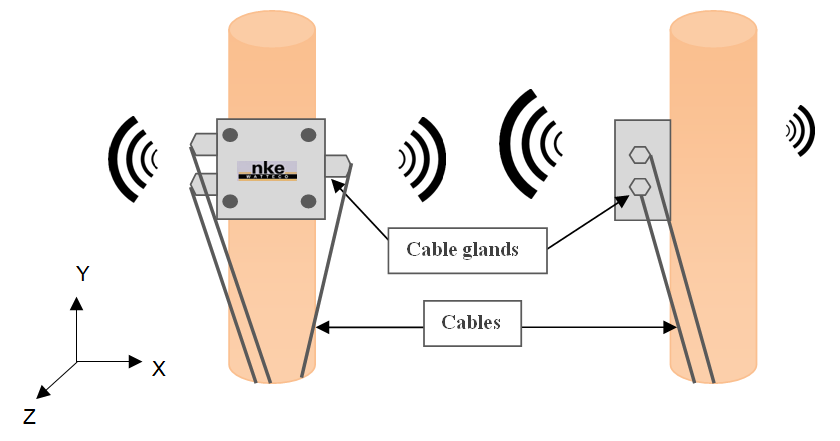
Autonomy
The information in the table below represents how long the battery can last. It is based on the default configuration at ambient temperature (+25°C) within the optimal operating range of the sensor via a LoRaWAN network (one uplink frame), when the spreading factor used is SF12. The disposable battery has a 3.6Ah capacity, of which 85% is used.
Transmission periodicity | Battery life |
---|---|
2 frames/ 24 hours | 10 years |
Human Machine Interface
The Press’O sensor has a buzzer that allows it to “communicate” with the user. A reed switch is available under the sticker. It is possible to use a magnet to activate it and makes specific actions on the sensor (Switch off, switch on, Re-associtation…). When the reed switch is activated, the buzzer rings quickly.
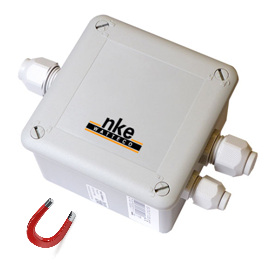
Switch ON (disable storage mode) | 1 second | |
Switch OFF (enable storage mode) | 5 seconds |
- Configuration: "void" frames are sent every minute for 10 minutes.
Way to trigger it | One passage of the magnet near the reed switch or specific ZCL command |
Way to stop it | Another passage of the magnet or specific ZCL command |
Effects on the sensor | |
Duration | The configuration mode lasts 10 minutes |
- A reassociation procedure can be requested if no downlink frame is received by the sensor during a given periodicity (4 days by default) or if a given number (100 by default) is reached or in case of failure (no acknowledgement received) by sending an applicative frame to the sensor or via the sensor’s IHM.
Way to trigger it | Three passages of the magnet near the reed switch or ZCL command from LoRaWAN cluster. |
Effects on the sensor |
- A factory reset is available on Watteco’s sensors. It deletes all the applicative settings saved in the flash memory (i.e. configured batches and reports will be deleted).
Way to trigger it | Two quick passages and a very long passage (until the sensor rings for the reset) of the magnet near the reed switch |
Effects on the sensor |
Applicative layer
The Press'O device implements “Analog Input” cluster associated to its Inputs. The link between the connectors and the EndPoint is given below:Codecs are available to decode frames: Downloads
Connector | End Point | Cluster | Unit |
---|---|---|---|
V+ | M/V- | 0 | Analog Input [4-20mA] | mA |
V+ | V- |M/V- | 1 | Analog Input [0-10V] | mV |
Cluster | Cluster name | Managed attributes |
---|---|---|
0x0000 | Basic | All |
0x0050 | Configuration | All Threshold is available with 3 slots |
0x8004 | LoRaWAN | All |
0x000C | Analog Input | All Threshold is available with 6 slots |
0x000F | Binary Input | All Threshold is available with 4 slots |
Default configuration
A default configuration is set:- The device reports the 4-20 mA value every 24 hours (EndPoint 0 / Cluster Analog Input / Attribute PresentValue) and the 0-10V value (EndPoint 1 / Cluster Analog Input / Attribute PresentValue).
Measurement periodicity
The measurement periodicity depends on the minimum recording interval. If the value of the minimum is 0, then the periodicity is 1 second. If the value of the minimum is different than 0, then this value is the same as the periodicity.Frame examples
All frames have to be sent on port 125
Standard report
Report
Report of the analog value of connector 4-20mA → Applicative payload is: 11 0a 00 0c 00 55 39 41 50 00 00 11: Fctrl (Endpoint=0) 41 50 00 00: present value ( single precision value =>13.0 mA)
Report of the analog value of connector 0-10V → Applicative payload is: 31 0a 00 0c 00 55 39 46 14 d0 00 31: Fctrl (Endpoint=1) 46 14 d0 00: present value ( single precision value =>9524.0 mV)
Configuration
Configure a standard report on the 4-20mA input Report immediately the measurement of the 4-20mA input on a 1mA variation. The measurement has to be reported at least every hour, and the measurement has to be made every 10 minutes. →The 4-20mA is the End Point 0, Cluster “Analog Input” is 0x000c, Attribute “PresentValue” is 0x0055. The maximum field has to be 0x0e10 to have a report every one hour and the minimum field has to be 0x800a to have a measurement every 10 minutes. The delta has to be configured to 0x3f800000 for a report every 1 mA variation. Applicative payload is: 11 06 00 0c 00 00 55 39 80 0a 80 3c 3f 80 00 00 11: Fctrl (Endpoint=0) 80 0a: minimum reporting interval (10 minutes) 80 3c: maximum reporting interval (1 hour) 3f 80 00 00: reportable change ( 1mA in single precision) →Response:11 07 00 0c 00 00 00 55 To disable the previous configuration, change the value of the minimum and maximum sending intervals and the delta to 0: 11 06 00 0c 00 00 55 39 00 00 00 00 00 00 00 00 or you can use remove report command. It is possible to create this configuration by using the inline encoder and this: { "EndPoint": 0, "Report": "Standard", "CommandID": "ConfigureReporting", "ClusterID": "AnalogInput", "ReportParameters": { "New": "No", "Reserved": 0, "CauseRequest": "No", "SecuredIfAlarm": "No", "Secured": "No", "NoHeaderPort": "No", "Batch": "No" }, "AttributeID": "PresentValue", "AttributeType": "SinglePrecision", "MinReport": { "Unit": "Minutes", "Value": 10 }, "MaxReport": { "Unit": "Minutes", "Value": 60 }, "Data": 1.0 }
Configure a standard report on the 0-10V input Report immediately the measurement of the 0-10V input on a 100mV variation. The measurement has to be reported at least every hour, and the measurement has to be made every 10 minutes. →The 0-10V is the End Point 1, Cluster “Analog Input” is 0x000c, Attribute “PresentValue” is 0x0055. The maximum field has to be 0x803C to have a report every one hour and the minimum field has to be 0x800a to have a measurement every 10 minutes. The delta has to be configured to 0x42c80000 for a report every 100 mV variation. Applicative payload is: 31 06 00 0c 00 00 55 39 80 0a 80 3c 42 c8 00 00
31: Fctrl (Endpoint=0) 80 0a: minimum reporting interval (10 minutes) 80 3c: maximum reporting interval (1 hour) 42 c8 00 00: reportable change ( 100mV in single precision) →Response:31 07 00 0c 00 00 00 55 To disable the previous configuration, change the value of the minimum and maximum sending intervals and the delta to 0: 31 06 00 0c 00 00 55 39 00 00 00 00 00 00 00 00 or you can use remove report command. It is possible to create this configuration by using the inline encoder and this: { "EndPoint": 1, "Report": "Standard", "CommandID": "ConfigureReporting", "ClusterID": "AnalogInput", "ReportParameters": { "New": "No", "Reserved": 0, "CauseRequest": "No", "SecuredIfAlarm": "No", "Secured": "No", "NoHeaderPort": "No", "Batch": "No" }, "AttributeID": "PresentValue", "AttributeType": "SinglePrecision", "MinReport": { "Unit": "Minutes", "Value": 10 }, "MaxReport": { "Unit": "Minutes", "Value": 60 }, "Data": 100.0 }
Configure a threshold on the 4-20mA input Report immediately the measurement of the 4-20mA Input when measure exceeds or falls a threshold of 10 mA with an hysteresis of +-1mA. The measurement has to be reported at least every hour, and the measurement has to be made every 10 minutes. →The 4-20mA is the End Point 1, Cluster “Analog Input” is 0x000c, Attribute “PresentValue” is 0x0055. The maximum field has to be 0x803C to have a report every one hour and the minimum field has to be 0x800a to have a measurement every 10 minutes. Applicative payload is: 11 06 000c 80 0055 39 800A 803C 70 41200000 3f800000 01
11: Fctrl (Endpoint=0) 80: new format frame 80 0a: minimum reporting interval (10 minutes) 80 3c: maximum reporting interval (1 hour)* 70: criteria slot 0, Threshold, No Alarm, OnExceed, OnFall 41200000: threshold of 10 mA 3f800000: hysteresis of 1 mA
01: number of occurences over the threshold before a report will be sent →Response:11 07 00 0c 00 00 00 55 To disable the previous configuration, change the value of the minimum and maximum sending interval and the delta to 0: 11 06 00 0c 00 00 55 39 00 01 02 03 or you can use remove report command. It is possible to create this configuration by using the inline encoder and this: { "EndPoint": 0, "Report": "Standard", "CommandID": "ConfigureReporting", "ClusterID": "AnalogInput", "ReportParameters": { "New": "Yes", "Reserved": 0, "CauseRequest": "No", "SecuredIfAlarm": "No", "Secured": "No", "NoHeaderPort": "No", "Batch": "No" }, "AttributeID": "PresentValue", "AttributeType": "SinglePrecision", "MinReport": { "Unit": "Minutes", "Value": 10 }, "MaxReport": { "Unit": "Minutes", "Value": 60 }, "Cause": [ { "CriteriaSlotDescriptor": { "Alarm": "No", "OnExceed": "Yes", "OnFall": "Yes", "Mode": "Threshold", "CriterionIndex": 0 }, "Value": 10.0, "Gap": 1.0, "Occurence": { "ExtendedOccurences": "No", "Occurences": 1 } } ], "Data": null }
Configure the duration of external power Configure a power duration of 500ms. Applicative payload is: 11 05 00 0c 80 03 21 01 F4
11: Fctrl (Endpoint=0) 01 F4: power duration ( 500ms) →Response:No response
It is possible to create this configuration by using the inline encoder and this: {"EndPoint": 0, "Report": "Standard", "CommandID": "WriteAttributeNoResponse", "ClusterID": "AnalogInput", "AttributeID": 32771, "AttributeType": "UInt16", "Data": 500}
Batch report
It is recommended to use this default parameters:Label (size = 3) | resolution | |
4-20 mA | 0 | 0.004 |
0-10V | 1 | 1 |
Battery Level | 2 | 100 |
External Power Level | 3 | 100 |
• Configure a batch report on analog input and voltage battery:
Timestamp and record the Voltage of a 0-10V sensor with a resolution of 1mV, a value has to be saved at least every 35 minutes or on a 5mV increase. Timestamp and record the battery voltage with a resolution of 0.5V, a value has to be saved at least every 24 hours. All data have to be concatenated and sent every 24 hours at the most.
→The EndPoint of 0-10V is 1, cluster "analog input" is 0x000C, and the attribute "PresentValue" is 0x0055
The battery voltage: Cluster « Configuration » is 0x0050, and attribute « Node power descriptor » is 0x0006.
For analog input, the delta is 0x40a00000(5mV in single precision), and resolution 0x3f800000 (1mV in single precision).
For the disposable battery power voltage the delta has to be set to 500=0x01F4 (0.5V),the resolution to 100=0x0064 (100mV),
Two frames must be sent to configure this batch.
Applicative payload of the present value of analog input 0-10V 31 06 00 0c 1d 00 55 00 80 01 80 23 40 a0 00 00 3f 80 00 00 0B 31: Fctrl (Endpoint=1) 1d: 0b00011101 => 0001110: size of configuration string after attribute ID (14 bytes) 80 01: minimum recording interval (measure every 1 minute) 80 23: maximum recording interval (35 minutes) 40 a0 00 00: required delta value (size: 4 bytes for attribute PresentValue => attribute type = 39, 5mV in single precision) 3f 80 00 00: required resolution (size: 4 bytes for attribute PresentValue => attribute type = 39, 1mV in single precision) 0B: tag value (ob00001011 => 00001: tag label 1, 011: tag size 3) →Response: 31 07 00 0c 00 01 00 55
Applicative payload of the battery voltage 11 06 00 50 15 00 06 04 80 0a 85 a0 01 F4 00 64 13
11: Fctrl (Endpoint=0) 15: 0b00010101 => 0001010: size of configuration string after attribute ID (10 bytes) 04: index of required field (Disposable battery) 80 0a: minimum recording interval (10 minutes) 85 a0: maximum recording interval (24 hours) 01 F4: required delta value (size: 2 bytes for attribute Node power descriptor => attribute type = 41, 0.5V) 00 64: required resolution (0.1V) 13: tag value (ob00010011=> 00010: tag label 2, 011: tag size 3) →Response: 11 07 00 50 00 01 06
To decode the batch reception, use the br_uncompress. Type for analog input is ST_FL (12) and is U16 (6) for the disposable battery power, so it is necessary to use this command:
echo "2015008001f4a24e7080d2de01421210f9ae295540bb656904" | ./br_uncompress -a 3 1,1,12 2,100,6
Result
UNCOMPRESS SERIE
cnt: 5 # Counter of the batch (from 0 to 7)
1605 # Timestamp in second of sending of the frame
# Format of data is: TimeStamp of Measure | Label | Value
1000 1 5052 # TimeStamp: 1000 s Label 1: Analog Input 0-10V Value: 5052 mV
1120 1 7520 # TimeStamp: 1120 s Label 1: Analog Input 0-10V Value: 7520 mV
1000 2 3600 # TimeStamp: 1000 s Label 2: Disposable battery Value: 3.6 V
1600 2 3500 # TimeStamp: 1600 s Label 2: Disposable battery Value: 3.5 V